By Mark Gibson, Operations Manager (Follow him on LinkedIn) &
Vince Jackson, Manufacturing Design Engineer
Why does it matter what kind of laser your fabricator uses?
A customer has to purchase the entire metal sheet provided by the material vendor. Especially with one-off pieces or longer runs, that’s where the hidden costs are when using older lasers.
Saying yes to rush jobs
Let’s say you have a rush job and your fabricator needs to figure out if they can do it. Labor shortages are very real so it can be hard to find more employees or do more overtime with existing staff.
So beyond labor, how can you reduce the amount of time to process the job during normal hours?
If you were to request a one-piece job that is 2x4 in. and is required to go on a 48x96 in. sheet, you would only use a quarter of it. The rest of that sheet gets wasted.
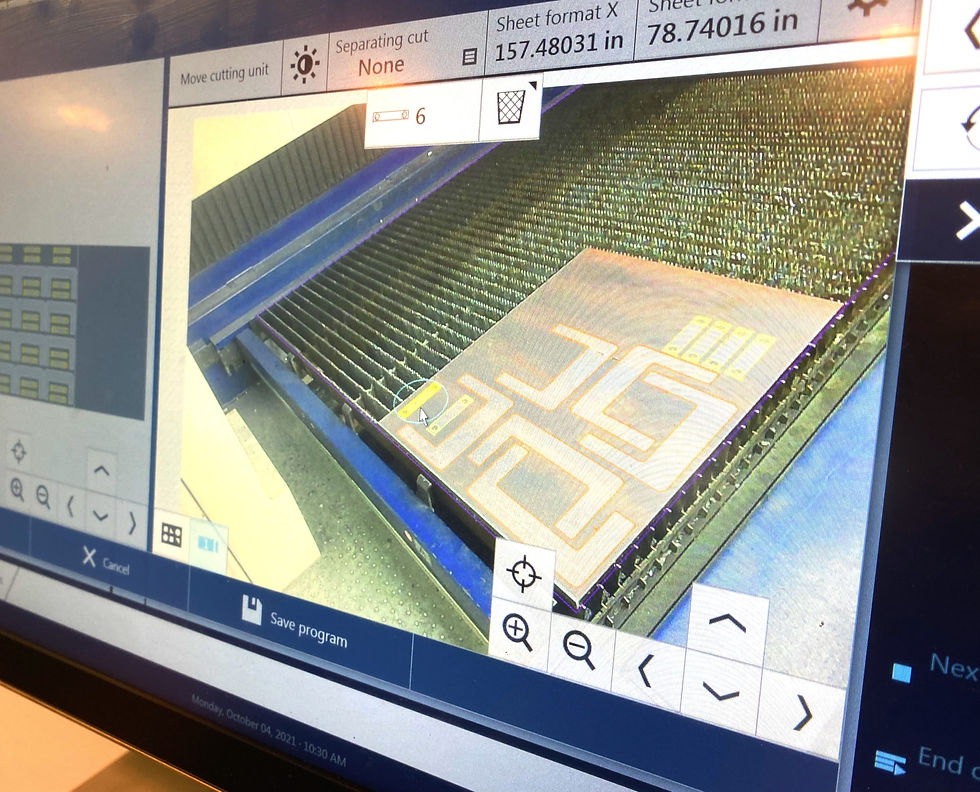
The manufacturing designer engineer will put the jobs out on the laser in queue. The above picture shows how our laser operator finds a place with the drag and drop option on our 8000-watt, Trumpf laser for rush or small volumes.
Reducing scrap
If you are thinking about pricing, your fabricator can reduce your cost by utilizing more of the sheet. This is especially important as you have longer runs to reduce wasted material costs.

In the above picture, the laser operator delineates where the sheet stops being used in order to save it for the next run rather than wasting it.
“The hands-on stuff like drag and drop at the machine is the art of fabrication that others can’t do,” - Design Manufacturing Engineer, who nests laser parts
How do customers add cost to their projects?
EXAMPLE 1: Adding fillets when cutting corners
When you are cutting corners, the laser comes to a point and it will pause.
You would put in additional radius dimensions also known as a fillet that is between .015-.003 based on the thickness of the material. The thicker the metal, the larger the radius that is needed. This ends up costing more with more material required.
Other lasers don’t cut with as sharp of corners so will waste more material. What’s important is the sizing will change. You need detail-oriented people to ensure they are thoroughly reviewing the design print to hit the targeted spec within the machine’s additionally required material specs.

In the above part design, it shows the difference between applying a radius versus keeping a sharp corner. The purpose of this is to eliminate time and material waste. Smoothing a corner by applying a radius will help eliminate blow outs and poor cuts.
EXAMPLE 2: Sending file types that need to be converted
Some engineers don’t realize that fabricators have to rebuild their design files. An example would be where a customer sent Valence STEP files and expected that it would be converted automatically and sent to the floor. STEP files aren’t drawn on sheet metal so those always need to be redrawn.
Our manufacturing design engineer had to redraw the STEP files in AutoCAD/Inventor files (our common manufacturing software across factories). He also found missing measurements since it was a 3D file but not a manufacturing file. Then, our manufacturing design engineer had to convert it into a “.GEO,” Trumpf specific, file.
When our design engineers have to open up files to transfer and continue to update dimensions, it adds costs.
Often times, a customer will say they don’t have to do this process with other vendors. However, it is more likely that it is happening with additional hidden costs but isn’t being communicated to the customer.
Why would Valence invest in a Trumpf laser over others?
The software is superior
Our sheet metal fabrication department can churn 75-100 unique part numbers per day in quantities of 1-1000. All with one design manufacturing engineer in the office who spends about an hour a day sorting by material, automatically nesting and generating the code.
Speed & thickness
Our 1000-watt Mazak laser can be used to cut shims and other simple jobs. The Trumpf laser is three times faster in speed. We use both machines but prefer the Trumpf for ‘hot,’ rush jobs and longer-runs.
Contour freedom
The bundled laser beam of a Trumpf laser only heats up the material locally, and the rest of the workpiece is subjected to minimal thermal stresses or not at all. This means the kerf, or the amount of material that is burned away, is barely wider than the beam. Even complex, intricate contours may be cut smoothly and free of burrs. Time-consuming post-processing is no longer necessary in most cases. Due to its flexibility, this cutting procedure is often used for small lot sizes, large variant ranges, and in prototype construction.
Valence’s laser capabilities
We've invested in both a Trumpf laser and a Mazak in our Sidney, Ohio location.
Dimensions
Trumpf Laser, 8000-watt laser, 72" x 144" Bed
1”- Mild Steel, 30" per min
1.12” – Stainless Steel, 6" per min
1” – Aluminum, 12" per min
.38” – Brass, 44" per min
.38” – Copper, 31" per min
Mazak, 1000-watt laser
48" x 96" Bed
1/4” – Mild Steel, 40" per min
1/4” – Galvanized, 40" per min
In our Lexington location, where we have a focus on machining, we've invested in the Messer Metal Master 2.0 plasma table.
Steel 5' x 10' x 1"
Aluminum 5' x 10' x 3/4"
Stainless 5' x 10' x 3/8"
Case study – reducing cost when laser cutting
The customer couldn’t move their production fast enough. With being such a widely known 165,000 square-foot facility that produced heavy duty harrows, rollers, cultivators, seeding machines, bale slicers and more farming equipment, the company was getting overwhelmed with backlog.
We laser cut ¼" to ¾" thickness 836 hot rolled steel.
How we saved for the customer?
The customer sent a file. Because we spent the extra time reviewing it, we found that it was layered and removed the additional layers prior to sending it through. It would have wasted additional materials. Because this is a customer that does ongoing longer runs of over $100k per month, this may have been missed by another fabricator trying to move fast enough to process everything on time. We were able to give those savings back to the customer.
Comments